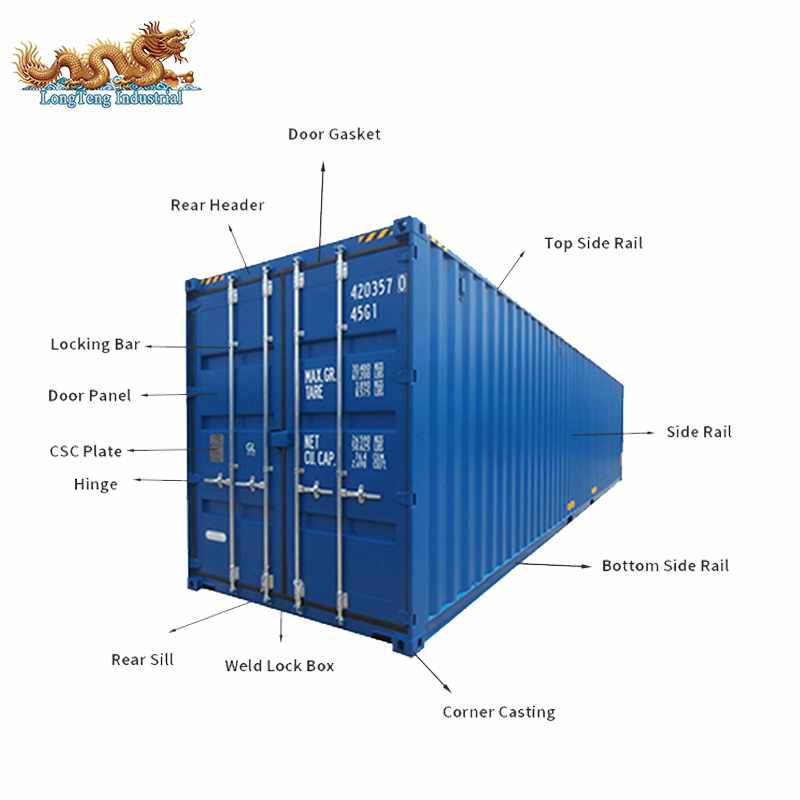
History of Sea Containers
Invented by Malcom Purcell McLean in 1956. Malcom Purcell McLean was an American truck driver and entrepreneur who was born in North Carolina in 1913.
The first transport of containers was recorded to have happened from the port of New York to the port of Houston, involving 58 aluminum containers.
However, containerization took its time to expand globally but not until 1966 when the US deployed McLean's invention in the Vietnam War.
What is Containerization
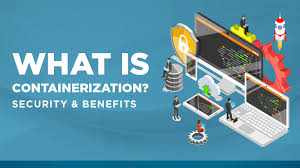
Simply, it is a term in the shipping industry that defines the practices and/or techniques used to unitize sea containers for storage and transport.
‘Unitizing’ is the implicit term for organize in the shipping industry as sea containers are stacked on each other at the ports and/or loaded in vessels for a voyage.
Advantages of Containerization
containerization was necessary to diminish the;
Cost of freight transportation by eliminating
The need for repeated handling of individual pieces of cargo (which frequently led to cargo damages),
Reduced cargo theft
Improved reliability and
Cut down inventory (Warehousing) costs by shortening transit times. Thus more goods were able to be moved from a warehouse to be shipped on a particular day than before.
Disadvantages of Containerization
Capital Intensive
Requirements for new technologies and handling equipments
Requirements for new trucks
Requirements for new Vessels as conventional vessels couldn't be used for containerized cargo.
Facilitated Contraband
Container consumes huge terminal space
Requirements for new berths, docks, and terminals
What is a Sea Container?
A standard intermodal structure of steel that is sea worthy and equipped with the necessary devices to facilitate its ready handling from one mode to another.
Operational features of a Sea Container
Must have an internal volume of 1m3
Durable for repeatable use
Must have an ISO number and CSC plate
Fitted with devices to facilitate its ready handling from one mode to another
Designed to be easily filled and emptied.
Features of a Sea Container
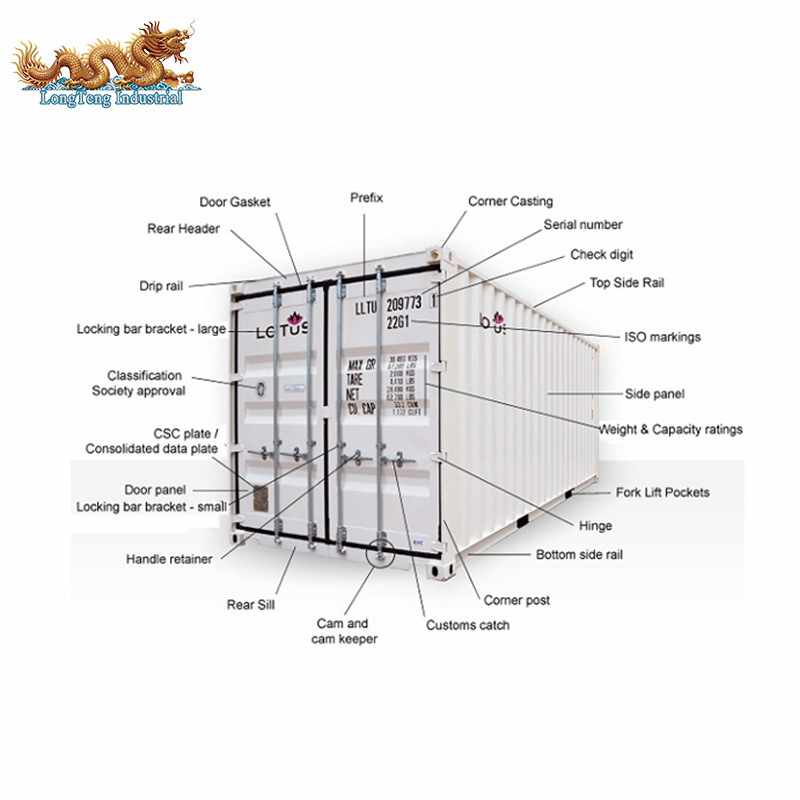
ISO number
CSC plate
Side wall panel
Floor
End doors
Corner casting and fittings
Tare and payload information
Forklift pockets
Roof panel
Container Identification
The ISO 6346 convention of 1966 is the standard that deals with coding, marking and identification of the container.
NB: The International Container Bereau (BIC) is responsible for the registration of all sea worthy containers.
The ISO then demands every container to have a series of identification marks and safety certification.
The safety certification is on the CSC (Container Safety Convention) plate.
The identification number is written on the top, sides, back (horizontally) and front (vertically) of the container and denotes;
Four letter codes ( first 3 letters are the owners code) and the last letter always represented either as U (ISO constant for all freight containers), or J (ISO constant for detachable freight containers and related equipments) or Z (ISO constant for all trailers and chassis)
6 digits followed by a check digits (which is used to validate if all the other codes are transmitted correctly). A two digits (size code) in the 6-digit code denotes the size (length and height) of the container. Whiles another two digits code (type code) in the 6-digits code denotes the special characteristics of the container.
Swap Body
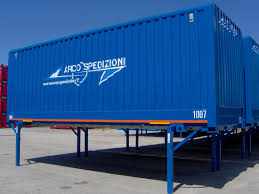
A detachable trucking system whereby the body of the truck can be lifted off the truck's chassis and placed on a railcar and/or piggyback system for transport to final destination where it is being lifted back unto another truck's chassis for final delivery. The swap body usually combines road and rail transport systems.
Hub and Spoke Systems
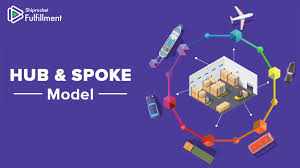
In a hub and spoke system of containerized maritime trade, cargo to a region is delivered first to a primary hub port and then transported to its final destination, whether by sea, rail, road or inland waterways. Incase by sea; the cargo is transhipped to its final destination by a feeder or a trans-shipment vessel.
Similarly, exports from the region are collected in the primary hub, and then transported to final destination.
NB:
Hub to Spoke - Distribution
Spoke to Hub - Collection
While these primary ports are often equipped to allow for a quick turnaround time of vessels, there are usually two primary characteristics that set them apart from other ports: the primary hubs:
(a) tend to be geographically central to the region and
(b) can accommodate larger vessels than other ports in the region.
Example of Hub Ports
Port of Shanghai, Port of Busan and Port of Rotterdam.
Advantages of the Hub and Spoke System
A better capacity utilization
Concentration of administrative and communication facilities
Minimized transaction costs and higher efficiency
Warehousing
Systems in the Hub and Spoke Systems
Trans-shipment hubs: must have deep water, high capacity and productivity, cranes to load and unload the biggest vessels and lastly must have minimum deviation from the main trade lanes. Eg. Deep-sea gateway ports and short-sea or intra regional ports.
Feeder Services: These are transport services which connect a hub or main container port with other minor ports in one ocean range
Landbridges: These are intercontinental railway networks that serve as a link in maritime transport chain and has its origin and destination in a foreign country. Eg. Silk route of China that connects Yiwu to Madrid and Trans-siberian railway, linking Moscow to China. They combine Sea, Road and Rail leg transports.
Mini-landbridges: These are international railway networks that serve as link in a transport chain and has its origin and destination in a foreign country. They combine road and rail leg transport only.
Piggy-back Transportation: involves the carriage of the whole trailer with container and/or vehicles by a special railway wagon system. It is preferred for economical and environmental benefits.
Contracts and Pricing in Container Transport
NB: Container operators and shipping lines are involved in container leasing because;
It financially saves them from manufacturing or buying their own containers
Avoid the transportation of empty containers
Adjust the container stocks in relations according to imbalances.
Leasing Arrangements: 1. One-way lease 2. Round way lease 3. Master leasing
Contracts terms:
1. Merchants haulage (shipper is responsible for pre and post carriage thus must arrange for a contract of affreightment with an MTO)
2. Carriers haulage ( pre and post carriage is the MTO's responsibility. The shipper have to only provide the cargo for loading and as such concludes only one multimodal contract with the MTO)
3. Mixed Arrangements.
Contents Checklist for Negotiating Service Contracts
Name of the sender (handled confident)
Ports of shipments and destination
Kind of freight (FCL or LCL)
Contracts or scale of rates
Opening and final dates
Service liability for the shipping company or MTO
Additional agreements, sanctions clauses.
Cost Structure in Maritime Transport
Main carriage 28%
Trans-shipment costs 39%
Pre and post carriage 20%
Additional costs 13%
Factors that affects Cost Structure
Terminal handling charges
Need for special handling equipments due to cargo nature.
Need for special stowage due to cargo nature
Voyage distance.
Warehousing charges
Surcharges
VGM
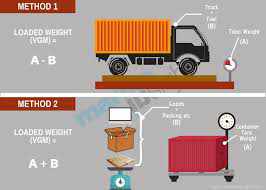
IMO ammended the Solas (International Convention for the Safety Of Life At Sea) and made it legally effective in 1st July 2016. Thus no container can be loaded unto a ship without a verified weight. The VGM is inspected by the terminal operator and the Carrier
The GSA (Ghana Standards Authority) is mandated by the Solas under IMO to ensure that all standards in weight verification are enforced; from the equipments being used in weighing (eg. weighbridges) to the calibration of the weighing equipments. The GSA is also involved in issuance of licenses to companies who operate weighbridges and weighing equipments
NB:
The responsibility to verify weight of the container for export lies in the hands of the shipper (person/institution in charge for the final packing of goods into the container) under the Solas
All containers meant for export must obtain a VGM from Standard Authority certified weighbridges only.
Container Seals
Container seals are door seals that are put on international shipping containers once a shipment is loaded. This seal is meant to stay on through to the container’s final destination before being removed by the consignee.
They can either be a bolt seal or a cable seal and each has its own unique number as identification that is listed on the shipping paperwork (male and female)
The most important part of having the seal, besides having it unbroken during the voyage, is that it is put in the correct place on the container. Thus the seal must be placed on either both lock rods or on one lock rods on the Sea Container doors
If for some reason the container is opened in transit this seal will be broken and the shipper will be told.
Before opening the container, the people who receive it must check the bill of lading to be sure the seal number matches with the one on the container they have received, it will have a series of letters and the numbers and all must match exactly or it could be different from the original seal.
If for some reason the seal number do not match, it is important to contact the shipping line right away and try to have the situation resolved. If possible you should not open or unload the container until you have a representative from the shipping line present.
Their participation is crucial in the event of a claim. In any event, the seal is critical part of a shipping container.
Not only is it there to protect the shipper, but it is just as important to the shipping line.
How Seal Number Discrepancies Happens
Typographical errors during typing manifest.
Improper capturing due to confusion caused by similar seal number patterns, (Seal number XYZU1234567 and XYZU1234566 could be two different seals).
Fraud committed by wilful usage of similar number patterns. E.g. of above.
Seal broken due to theft/pilferage and a new seal with a different number is now on the container.
Seal broken due to Customs inspection and then resealed but manifest not amended.
Steps To Take When There's Any Discrepancy
Immediately advise the shipper of this discrepancy and check if there could have been any mistakes from their side with regards to the seal number they provided to the shipping line or if provided by shipping line.
Advise the shipping line of this discrepancy and if point 1. Above has been cleared with the shipper, then put the shipping line on notice for all costs, consequences, damages and claims as the seal was correct when it was handed over to the shipping line at the port of loading.
Notify the shipping line of your intention to conduct a joint survey of the condition of the contents of the container in order to ascertain any issues such as pilferage, theft, damage or loss of cargoes
Notify your insurance company of potential loss of cargo or damage to cargo and follow their instructions.
Purpose of Container Outside and Inside Variation
Outside dimensions is for ease of transportation with regards handling and stacking
Inside dimensions are for stowage factor, optimization of volume and compliance to regulatory demands like VGM
There are 3 weight measurements associated with shipping container trade
Rating: permissible allowed maximum weight - weight of container and it contents.
Tare weight: weight of empty container 20ft tare is b/n 1.8tons - 2.4tons and 40ft tare is 2.8tons - 4tons
Payload: maximum permissible allowed weight for contents to be loaded into the container including dunnages.
Loading Plan Considerations
Essential to ensure that packed goods in the container are protected against movements. (this is necessary to protect the goods from damages and the personnel when the unit is opened for discharge).
Each type of commodity to be transported requires special stowage considerations and securing methods.
Weight distribution: Spread the weight evenly over the entire area of the floor of the box
Space utilization: Use the whole space wall to wall, filling empty spaces with dunnages.
Write a comment ...